An exclusive look inside Skookumchuck Pulp Inc.
Learn about the pulp industry with this visual primer
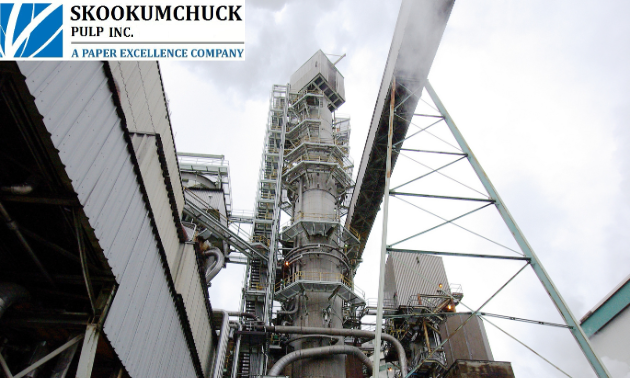
The tall vessel in the centre is the continuous Kamyr digester in which wood chips are surrounded by alkaline liquor and “cooked” at high temperature for a couple of hours. This cooking process digests (breaks down) the lignin (or glue) which holds the cellulose fibres together. Pulp is then blown out at the bottom of the digester. — Robert Hawkins photo
Have you ever wondered how pulp is created and what a mill looks like inside and out? If so, this photo essay of Skookumchuck Pulp Inc. is for you. Scroll down to see the inner workings of this fascinating industry. Photos were taken by Kootenay Business’s Robert Hawkins. Special thanks goes out to Roger Puar, technical manager at Skookumchuck Pulp Inc., for providing the photo descriptions.
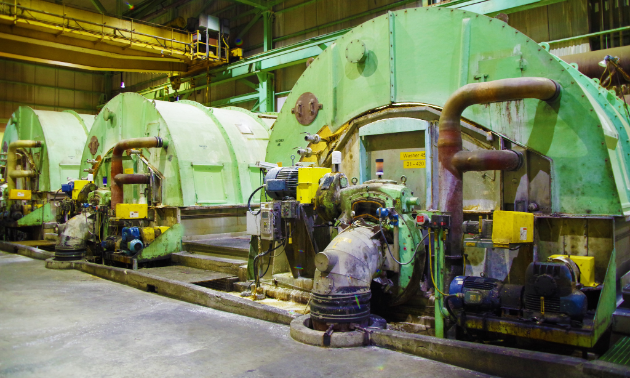
Bleach plant vacuum drum washers remove the bleaching chemicals and dissolved lignin from the pulp. — Robert Hawkins photo
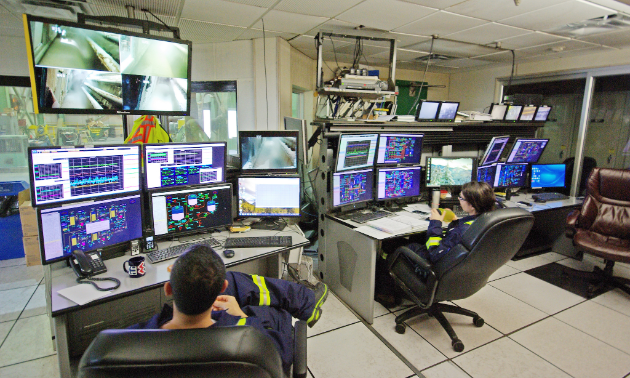
Pulp mill control room operators monitor and control the operation of digesters, screening equipment, washing equipment and other pulp processing equipment via an automated distributed control system (DCS). The DCS, along with video monitors, is used to ensure pulp processes are operating within key process parameters. — Robert Hawkins photo
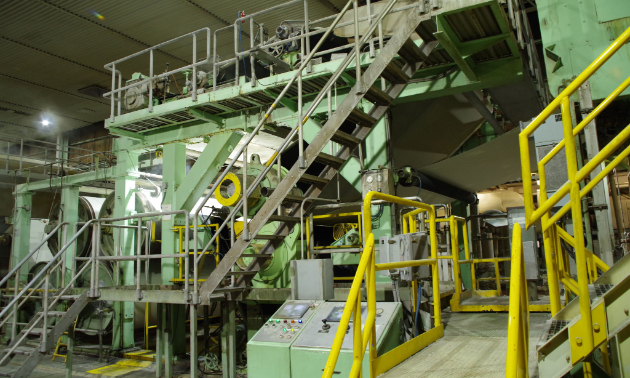
The wet pulp sheet travels through three press sections on the pulp machine to remove water prior to the pulp sheet entering the dryer. The sheet still contains approximately 53 to 55 per cent water by weight. — Robert Hawkins photo
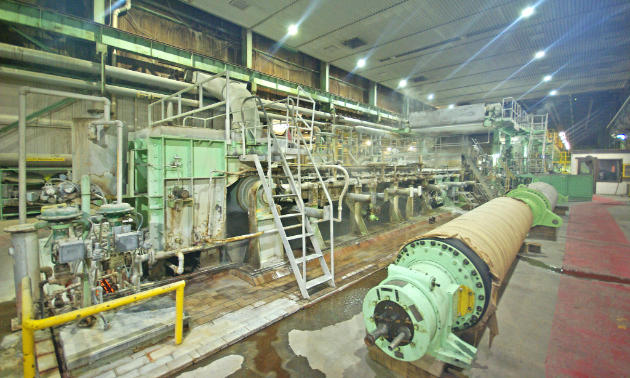
The first section of the pulp machine (wet end) is shown. A dilute slurry of bleached pulp stock is sprayed onto a Fourdrinier forming wire where the water is drained and vacuumed from the pulp fibres, leaving behind a wet web. The water is recycled and used in other stages of the pulp-making process. — Robert Hawkins photo
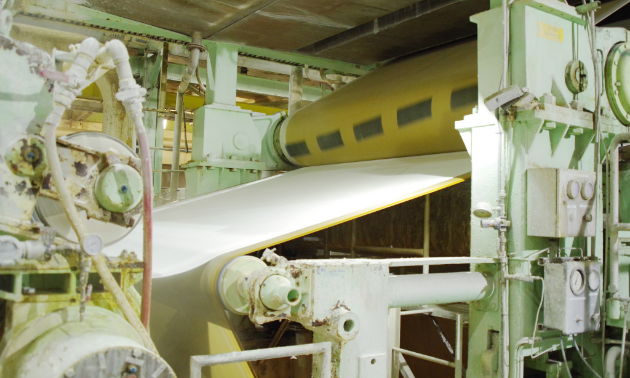
The second section of the pulp machine is where the wet fibre web passes between large rolls loaded under high pressure to squeeze out as much water as possible. The sheet is supported by press felts that maximize water absorption. Fibre-to-fibre bonding is improved, which increases the sheet's strength. — Robert Hawkins photo
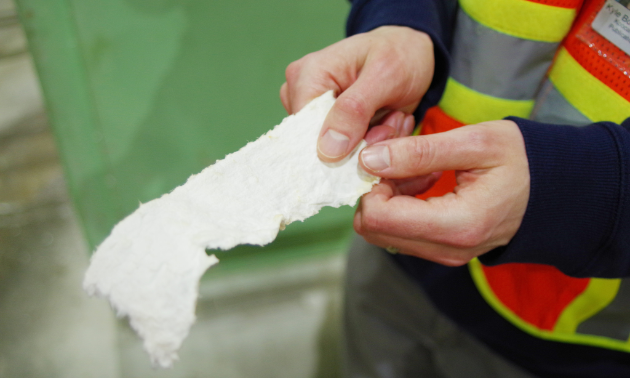
Northern Bleached Softwood Kraft (NBSK) pulp is shown. When added to warm water, the pulp sheet readily dissolves into individual fibres and can be mixed with other types of fibres (mechanical, recycled, etc.) at the customer’s end to produce various value-added products. — Robert Hawkins photo
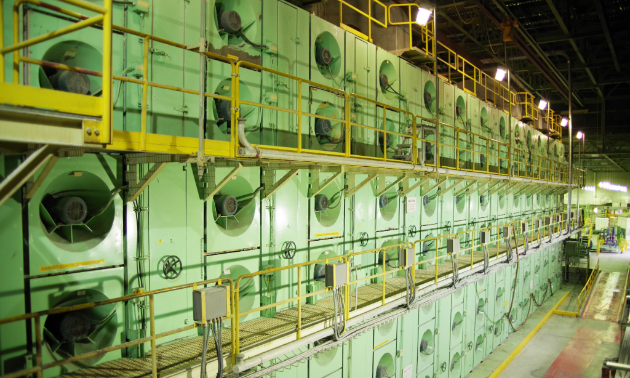
The pulp sheet dryer is shown. The pulp sheet discharged from the third press nip undergoes 27 passes in the Flakt dryer. The Flakt dryer increases the sheet consistency from approximately 46 per cent (containing 54 per cent water) to 90 per cent air dry content (containing 10 per cent water). Residual water in the pulp sheets ensures integrity and prevents cracking due to dryness. — Robert Hawkins photo
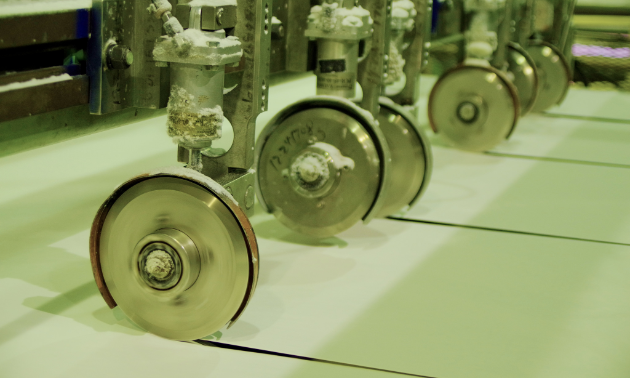
High-speed circular slitter knives cut the pulp sheet coming out of the dryer to the desired sheet width. The sheets are then cut in the cross direction to produce a stack of individual sheets called bales. — Robert Hawkins photo
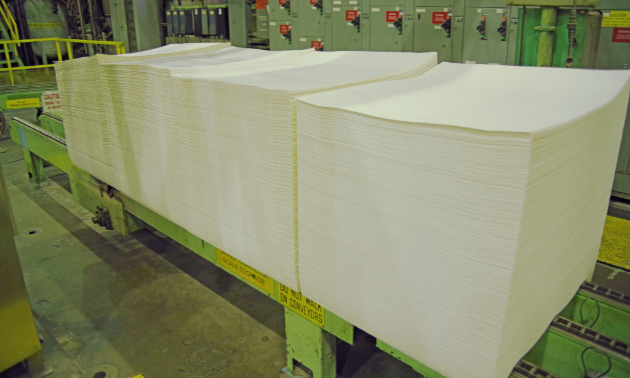
Bales of pulp consist of stacked pulp sheets. The bales undergo significant compression through the bale press before being wrapped in two sheets of kraft pulp and tied with galvanized wire. Each bale weighs approximately 245 kilograms. — Robert Hawkins photo
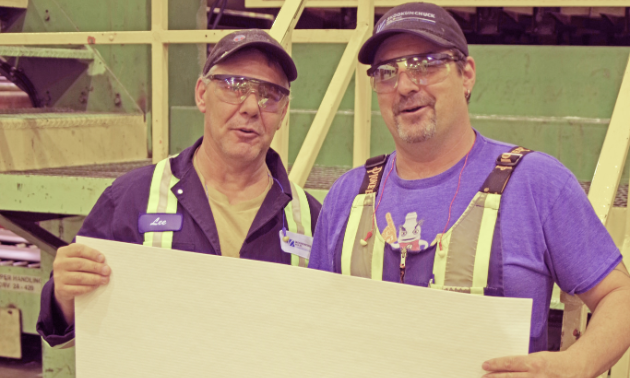
(L to R) Lee Spence and Wilf Davis, employees of Skookumchuck Pulp Inc., hold a sheet of high-quality Northern Bleached Softwood Kraft (NBSK) pulp. These sheets of pulp, measuring 86 centimetres by 74 centimetres, are stacked together to produce bales of pulp. Each bale weighs approximately 245 kilograms. — Robert Hawkins photo
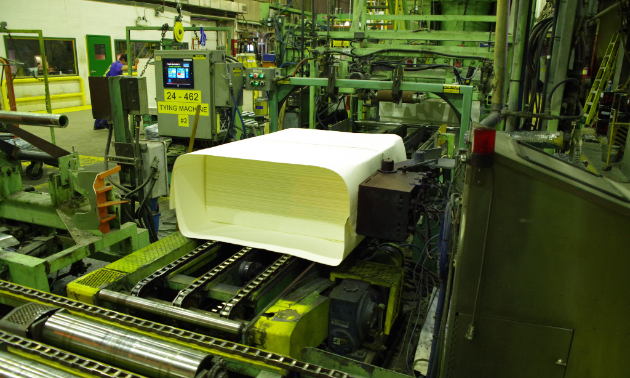
The compressed bales of pulp are wrapped in two sheets of kraft pulp (produced at the mill site) and tied with galvanized wire. The open ends are then folded and tied with a second tying wire. — Robert Hawkins photo
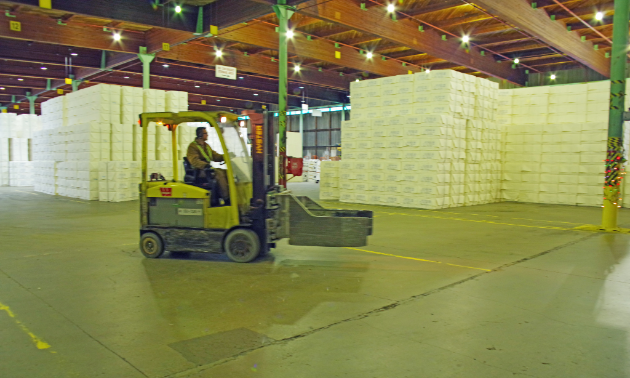
The final product, unitized bales of pulp, is shown stored in the warehouse. The pulp is loaded into rail cars and shipped directly to domestic customers or taken to port where they are loaded into cargo ships that transport them to overseas clients. — Robert Hawkins photo
Comments